So I’ve asked this question already but the answer I got wasn’t very clear at all. I’ve highlighted the picture so that you can see more specifically what I’m asking. In the first picture were the machine hours, direct labor hours, total fixed manufacturing overhead, variable manufacturing overhead per machine hour, variable manufacturing overhead per direct labor hour is all listed- I know I use those numbers in the equation that is on the bottom of the page, the predetermined overhead rate formula. My question is regarding the chart that is in the middle of that page. It is titled job 407 and it lists machine hours as 90 for milling And 4 for assembly. Underneath that it lists direct labor hours as 5 for milling and 20 for assembly. I am asking specifically where those numbers have come from and how they have calculated those amounts. I have highlighted the charts for you.
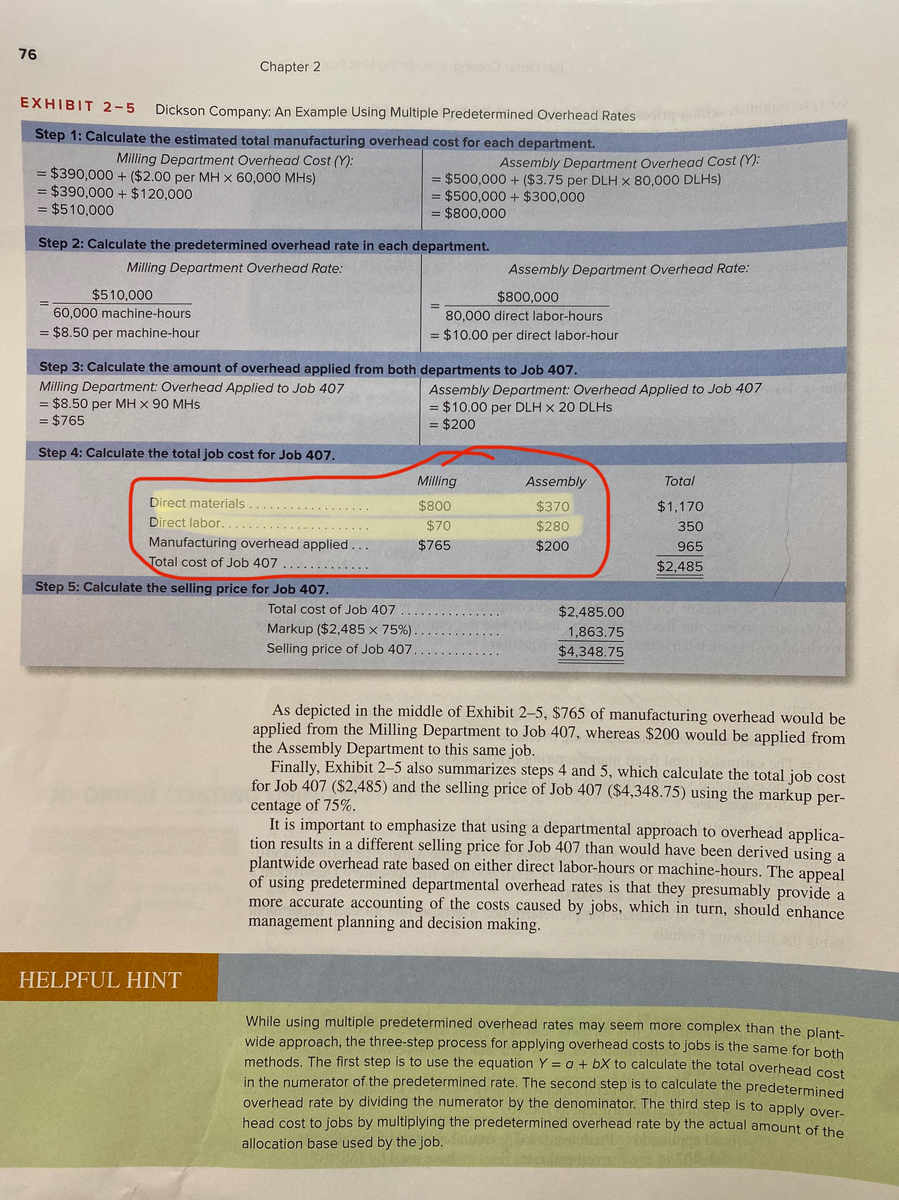
Extracted text: 76 Chapter 2 ebode EXHIBIT 2-5 Dickson Company: An Example Using Multiple Predetermined Overhead Rates Step 1: Calculate the estimated total manufacturing overhead cost for each department. Milling Department Overhead Cost (Y): Assembly Department Overhead Cost (Y): = $390,000 + ($2.00 per MH x 60,000 MHs) = $390,000 + $120,000 = $510,000 = $500,000 + ($3.75 per DLH x 80,000 DLHS) = $500,000 + $300,000 $800,000 Step 2: Calculate the predetermined overhead rate in each department. Milling Department Overhead Rate: Assembly Department Overhead Rate: $510,000 60,000 machine-hours $800,000 80,000 direct labor-hours = $8.50 per machine-hour = $10.00 per direct labor-hour Step 3: Calculate the amount of overhead applied from both departments to Job 407. Milling Department: Overhead Applied to Job 407 = $8.50 per MH x 90 MHs = $765 Assembly Department: Overhead Applied to Job 407 = $10.00 per DLH x 20 DLHs = $200 Step 4: Calculate the total job cost for Job 407. Milling Assembly Total Direct materials $800 $370 $1,170 ...... ..... Direct labor $70 $280 350 Manufacturing overhead applied ... Total cost of Job 407 ............. $765 $200 965 $2,485 Step 5: Calculate the selling price for Job 407. Total cost of Job 407 $2,485.00 Markup ($2,485 x 75%) 1,863.75 Selling price of Job 407 $4,348.75 As depicted in the middle of Exhibit 2-5, $765 of manufacturing overhead would be applied from the Milling Department to Job 407, whereas $200 would be applied from the Assembly Department to this same job. Finally, Exhibit 2-5 also summarizes steps 4 and 5, which calculate the total job cost for Job 407 ($2,485) and the selling price of Job 407 ($4,348.75) using the markup per- centage of 75%. It is important to emphasize that using a departmental approach to overhead applica- tion results in a different selling price for Job 407 than would have been derived using a plantwide overhead rate based on either direct labor-hours or machine-hours. The appeal of using predetermined departmental overhead rates is that they presumably provide a more accurate accounting of the costs caused by jobs, which in turn, should enhance management planning and decision making. HELPFUL HINT While using multiple predetermined overhead rates may seem more complex than the plant- wide approach, the three-step process for applying overhead costs to jobs is the same for both methods. The first step is to use the equation Y = a + bX to calculate the total overhead cost in the numerator of the predetermined rate. The second step is to calculate the predetermined overhead rate by dividing the numerator by the denominator. The third step is to apply over- head cost to jobs by multiplying the predetermined overhead rate by the actual amount of the allocation base used by the job.
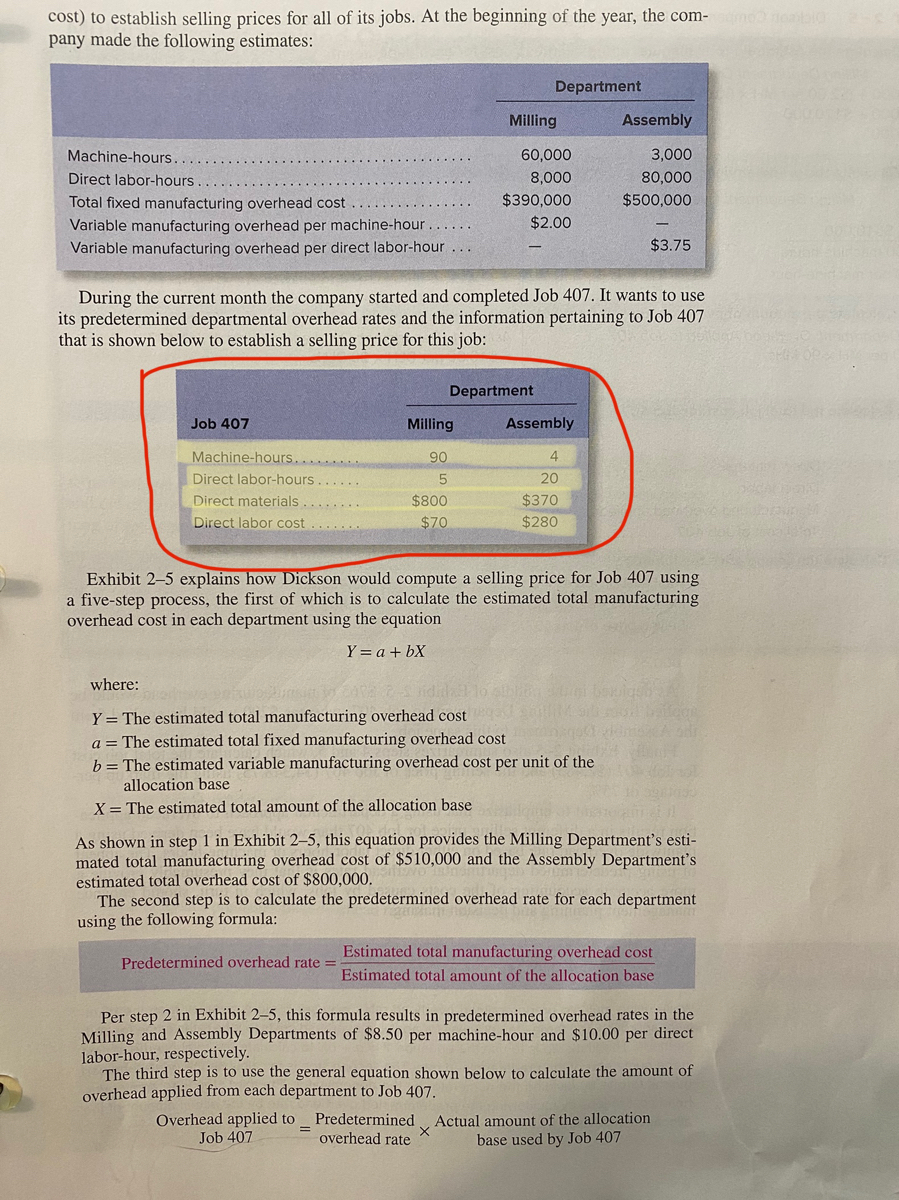
Extracted text: cost) to establish selling prices for all of its jobs. At the beginning of the year, the com- neabig pany made the following estimates: Department Milling Assembly Machine-hours. 60,000 3,000 Direct labor-hours 8,000 80,000 $390,000 $500,000 Total fixed manufacturing overhead cost Variable manufacturing overhead per machine-hour $2.00 Variable manufacturing overhead per direct labor-hour ... $3.75 During the current month the company started and completed Job 407. It wants to use its predetermined departmental overhead rates and the information pertaining to Job 407 that is shown below to establish a selling price for this job: Department Job 407 Milling Assembly Machine-hours....... 90 4 Direct labor-hours 20 Direct materials.... Direct labor cost $800 $370 $70 $280 Exhibit 2-5 explains how Dickson would compute a selling price for Job 407 using a five-step process, the first of which is to calculate the estimated total manufacturing overhead cost in each department using the equation Y = a + bX where: Y = The estimated total manufacturing overhead cost a = The estimated total fixed manufacturing overhead cost b= The estimated variable manufacturing overhead cost per unit of the allocation base X = The estimated total amount of the allocation base As shown in step 1 in Exhibit 2–5, this equation provides the Milling Department's esti- mated total manufacturing overhead cost of $510,000 and the Assembly Department's estimated total overhead cost of $800,000. The second step is to calculate the predetermined overhead rate for each department using the following formula: Estimated total manufacturing overhead cost Predetermined overhead rate = Estimated total amount of the allocation base Per step 2 in Exhibit 2–5, this formula results in predetermined overhead rates in the Milling and Assembly Departments of $8.50 per machine-hour and $10.00 per direct labor-hour, respectively. The third step is to use the general equation shown below to calculate the amount of overhead applied from each department to Job 407. Overhead applied to Predetermined overhead rate Actual amount of the allocation base used by Job 407 Job 407