I need the answer in
Python
at least within
6 hours.
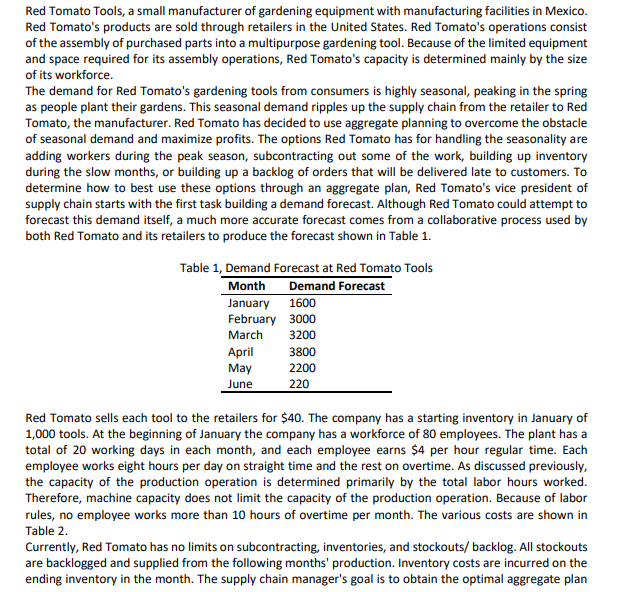
Extracted text: Red Tomato Tools, a small manufacturer of gardening equipment with manufacturing facilities in Mexico. Red Tomato's products are sold through retailers in the United States. Red Tomato's operations consist of the assembly of purchased parts into a multipurpose gardening tool. Because of the limited equipment and space required for its assembly operations, Red Tomato's capacity is determined mainly by the size of its workforce. The demand for Red Tomato's gardening tools from consumers is highly seasonal, peaking in the spring as people plant their gardens. This seasonal demand ripples up the supply chain from the retailer to Red Tomato, the manufacturer. Red Tomato has decided to use aggregate planning to overcome the obstacle of seasonal demand and maximize profits. The options Red Tomato has for handling the seasonality are adding workers during the peak season, subcontracting out some of the work, building up inventory during the slow months, or building up a backlog of orders that will be delivered late to customers. To determine how to best use these options through an aggregate plan, Red Tomato's vice president of supply chain starts with the first task building a demand forecast. Although Red Tomato could attempt to forecast this demand itself, a much more accurate forecast comes from a collaborative process used by both Red Tomato and its retailers to produce the forecast shown in Table 1. Table 1, Demand Forecast at Red Tomato Tools Demand Forecast 1600 Month January February 3000 March 3200 April May 3800 2200 June 220 Red Tomato sells each tool to the retailers for $40. The company has a starting inventory in January of 1,000 tools. At the beginning of January the company has a workforce of 80 employees. The plant has a total of 20 working days in each month, and each employee earns $4 per hour regular time. Each employee works eight hours per day on straight time and the rest on overtime. As discussed previously, the capacity of the production operation is determined primarily by the total labor hours worked. Therefore, machine capacity does not limit the capacity of the production operation. Because of labor rules, no employee works more than 10 hours of overtime per month. The various costs are shown in Table 2. Currently, Red Tomato has no limits on subcontracting, inventories, and stockouts/ backlog. All stockouts are backlogged and supplied from the following months' production. Inventory costs are incurred on the ending inventory in the month. The supply chain manager's goal is to obtain the optimal aggregate plan
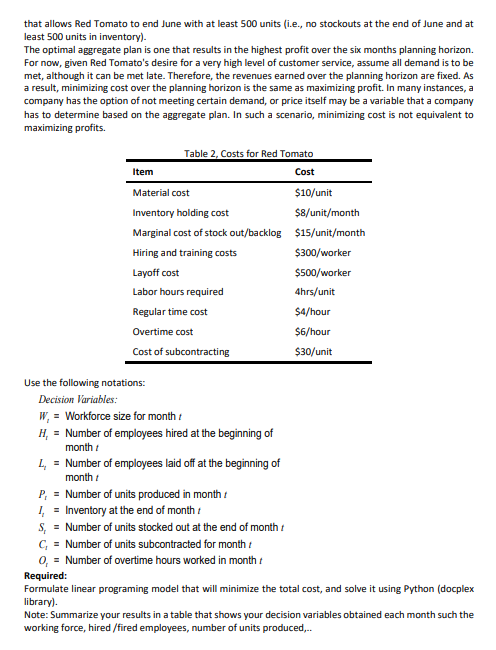
Extracted text: that allows Red Tomato to end June with at least 500 units (i.e., no stockouts at the end of June and at least 500 units in inventory). The optimal aggregate plan is one that results in the highest profit over the six months planning horizon. For now, given Red Tomato's desire for a very high level of customer service, assume all demand is to be met, although it can be met late. Therefore, the revenues earned over the planning horizon are fixed. As a result, minimizing cost over the planning horizon is the same as maximizing profit. In many instances, a company has the option of not meeting certain demand, or price itself may be a variable that a company has to determine based on the aggregate plan. In such a scenario, minimizing cost is not equivalent to maximizing profits. Table 2, Costs for Red Tomato Item Cost Material cost $10/unit Inventory holding cost $8/unit/month Marginal cost of stock out/backlog $15/unit/month Hiring and training costs $300/worker Layoff cost $500/worker Labor hours required 4hrs/unit Regular time cost $4/hour Overtime cost $6/hour Cost of subcontracting $30/unit Use the following notations: Decision Variables: W, = Workforce size for month : H, = Number of employees hired at the beginning of month : L, = Number of employees laid off at the beginning of month : P, = Number of units produced in month : I, = Inventory at the end of month i S, = Number of units stocked out at the end of month : C, = Number of units subcontracted for month : 0, = Number of overtime hours worked in month : Required: Formulate linear programing model that will minimize the total cost, and solve it using Python (docplex library). Note: Summarize your results in a table that shows your decision variables obtained each month such the working force, hired /fired employees, number of units produced,.