Please answer highlighted portion. Thank you.
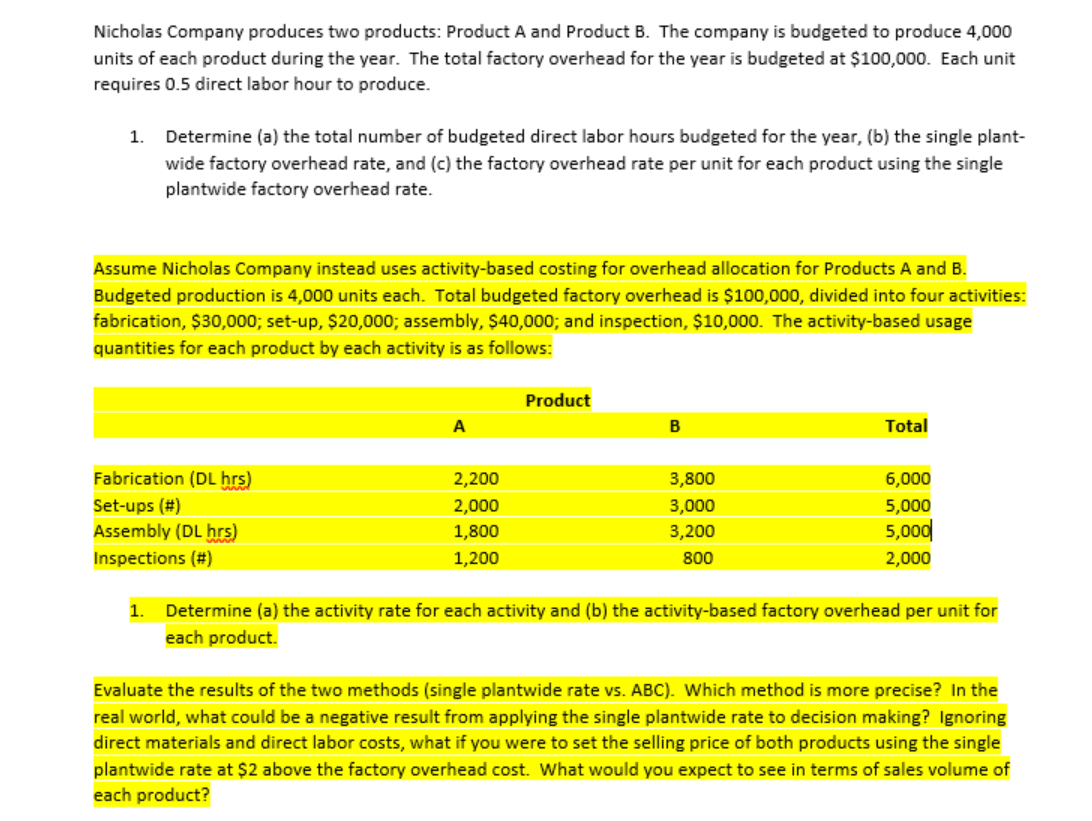
Extracted text: Nicholas Company produces two products: Product A and Product B. The company is budgeted to produce 4,000 units of each product during the year. The total factory overhead for the year is budgeted at $100,000. Each unit requires 0.5 direct labor hour to produce. 1. Determine (a) the total number of budgeted direct labor hours budgeted for the year, (b) the single plant- wide factory overhead rate, and (c) the factory overhead rate per unit for each product using the single plantwide factory overhead rate. Assume Nicholas Company instead uses activity-based costing for overhead allocation for Products A and B. Budgeted production is 4,000 units each. Total budgeted factory overhead is $100,000, divided into four activities: fabrication, $30,000; set-up, $20,000; assembly, $40,000; and inspection, $10,000. The activity-based usage quantities for each product by each activity is as follows: Product Total Fabrication (DL hrs) 2,200 3,800 6,000 Set-ups (#) 2,000 3,000 5,000 Assembly (DL hrs) 1,800 3,200 5,000 Inspections (#) 1,200 800 2,000 1. Determine (a) the activity rate for each activity and (b) the activity-based factory overhead per unit for each product. Evaluate the results of the two methods (single plantwide rate vs. ABC). Which method is more precise? In the real world, what could be a negative result from applying the single plantwide rate to decision making? Ignoring direct materials and direct labor costs, what if you were to set the selling price of both products using the single plantwide rate at $2 above the factory overhead cost. What would you expect to see in terms of sales volume of each product?